

Products in foam
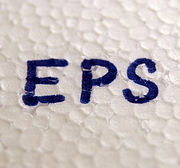
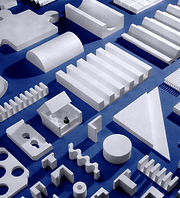
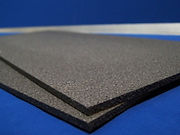
Styrofoam EPS: Expanded polystyreen
EPS, Airpop or Styrofoam (which is the tradename used for EPS by the Dow chemical company) is a hard foam with a closed cell structure. In spite of being very light-weight, expanded polystyrene (EPS) is relatively speaking very strong, it is quite elastic and yet exceptionally stable. For this reason it has a high shock-absorbing capability and can be milled very easily. EPS insulates exceptionally well, absorbs practically no moisture and is resistant to most salts, acids and oils. EPS can only be painted with waterbased paint (not with polyester or solvent based paints or coatings).
Expanded polystyrene is distinguished by a favourable price/quality ratio. The standard quality is a self-extinguishing version. Styrofoam is obtainable in very many different hardnesses so the impressionability can be selected in accordance with the application. It can be used in a very environmentally responsible way, it is absolutely CFK-free, it is produced with low energy consumption and is completely recyclable in pure condition. It is also extremely hygienic and may come directly in contact with food products.
EPS is processed in our own company starting with blocks. From these blocks, products are produced by means of hotwire cutting, milling, lathe work, etc. After that, assembly can also occur if required. All waste and residue materials resulting from production are processed into granules in the factory and are completely recycled in the production of impact-resistant polystyrene.
Neopor: Styrofoam with graphite
EPS exists also in a grey color, called Neopor. This is styrofoam with added graphite for increased insulation (up to 20%). The same qualities apply to Neopor and it can also be
cut with hotwire in planks, simple contours and milled into complex shapes.



Als opvulstuk voor meubelverpakkingen

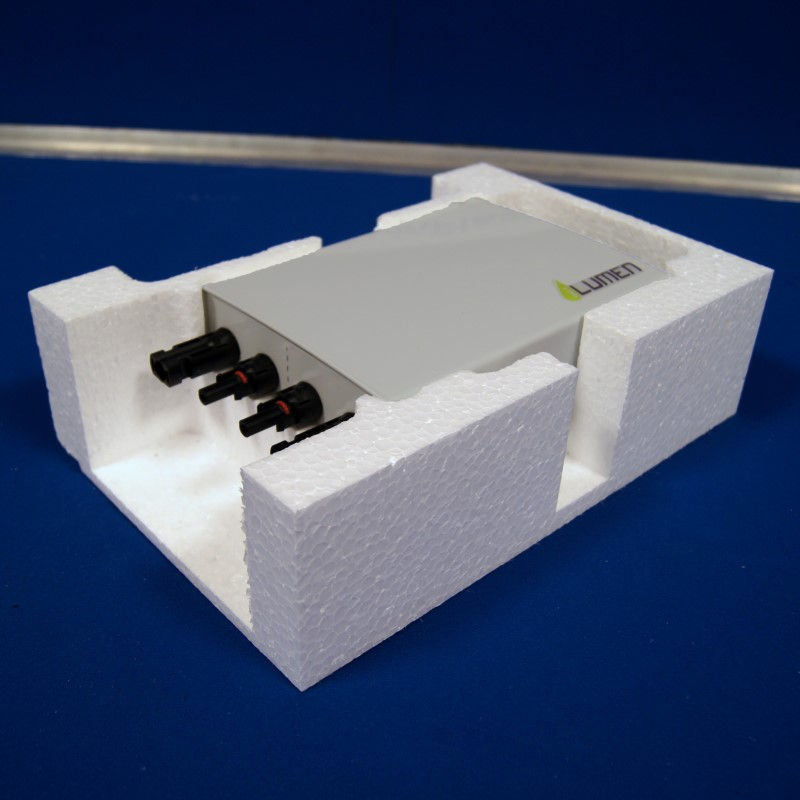
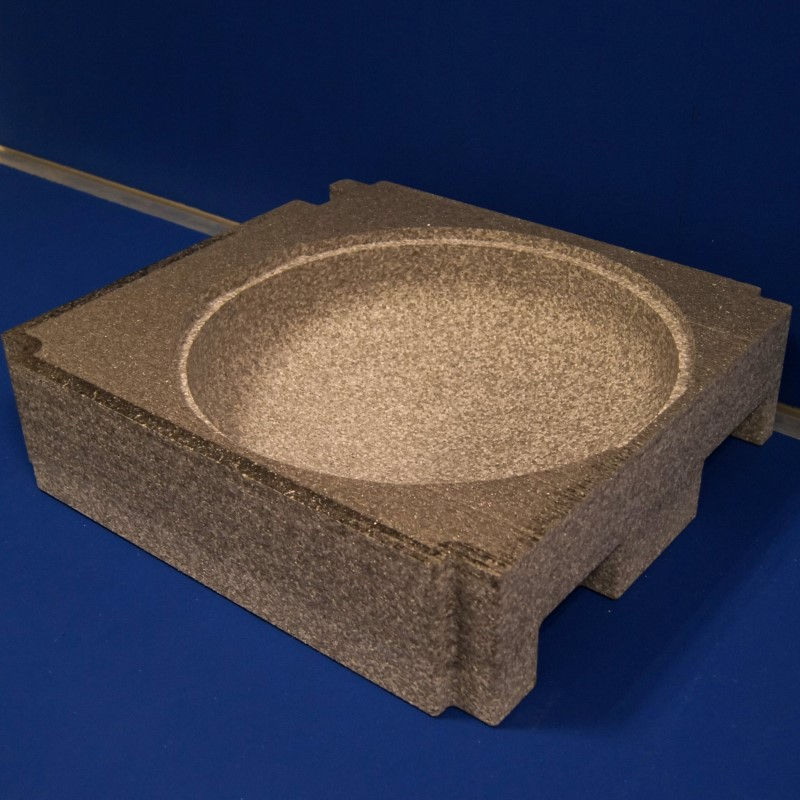
.
EPE / EPP
EPE (or expanded polyethylene) and EPP (of expanded polypropylene) are light and flexible foams, that offer very good shock-absorption (what makes them ideal for shock resisting packaging). This is because they can press together and distribute the force of impact over a larger surface because of this. Because they can be pressed together rather easy, they are less suited for a heavy, continuing type of pressure (for this EPS is much better suited).
Contrary to EPS, breaking or shape distortion does not happen to EPE and EPP, not even after multiple shocks. Softfoams like EPE and EPP restore themselves to their original shape after impact. EPE/EPP are suited for low (till -60°C) as high temperatures (until 100°C). Furthermore, they do not absorb water and float on water.
Twinplast uses EPE in 2 densities (25 and 42kg/m³) and in the colours white and black (by addition of carbon). EPP is slightly tougher and is used in heavier densities. EPE/EPP gets contour sawn or milled by Twinplast for (amongst others) shock-absorbing packaging for car parts, furniture protection or industrial parts.
Characteristics:
-
Light and strong
-
Flexible and compressible
-
Recovers fast and completely after compression
-
low warmth conduction and good insulation
-
Not water absorbing and floats on water
-
Doesn't break easily.
-
Sound absorbing
-
can be painted
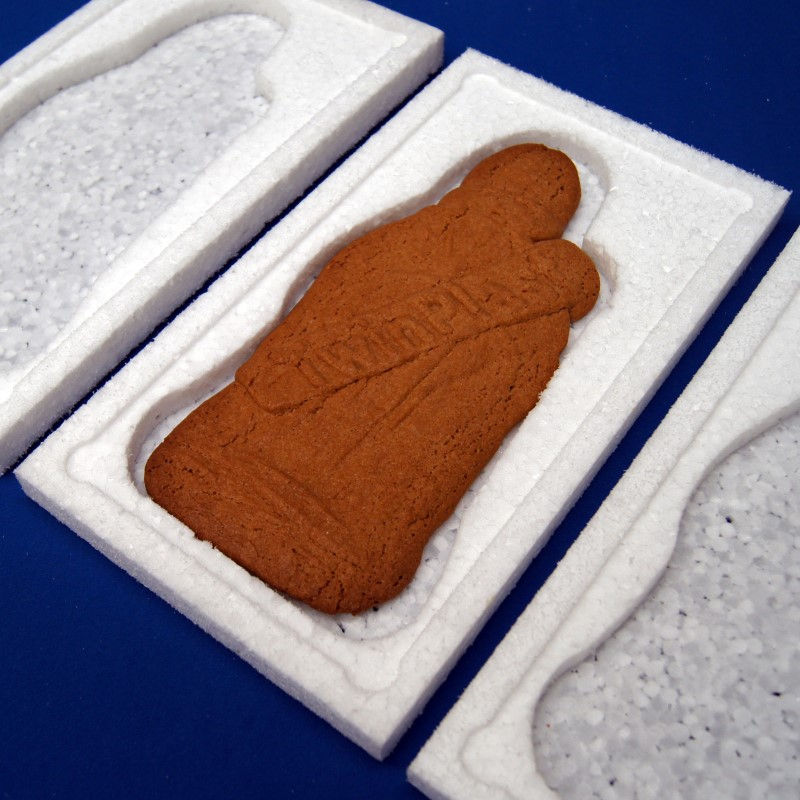
Verpakking voor speculaas met Twinplast in gebakken. (De vorm in hout werd ook door ons gefreesd.)

Oplegsteunen voor kwetsbare carrosserie-onderdelen intern te transporteren zodat ze niet gekrast worden.

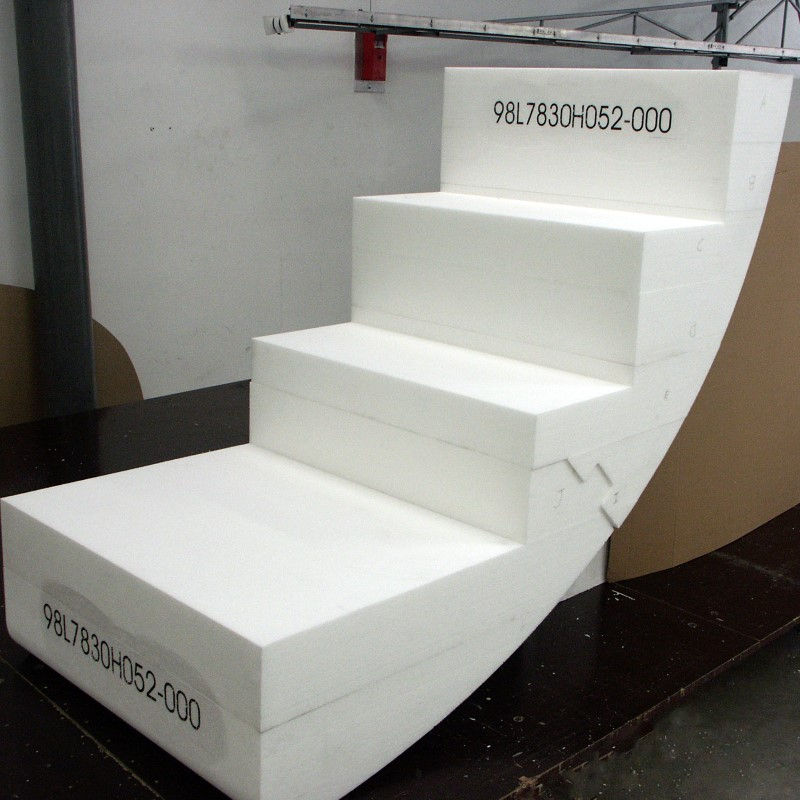
Trap voor in een vliegtuig.
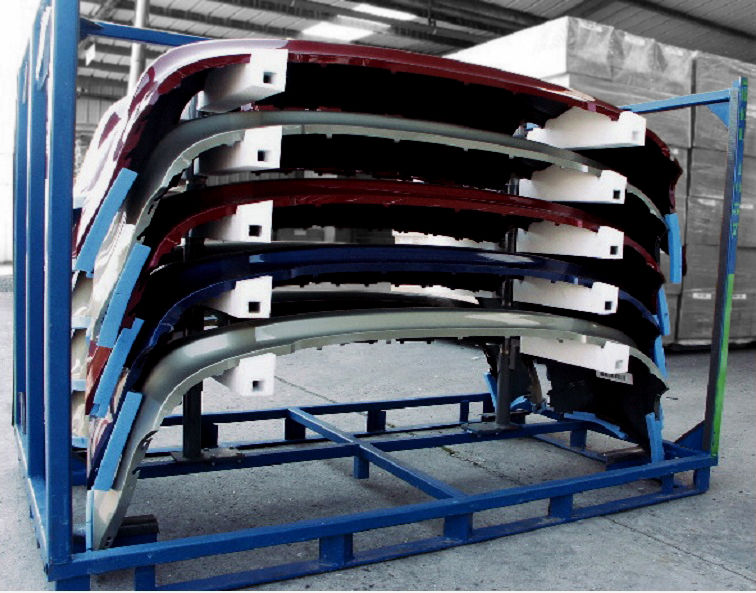
Verpakkingsartikelen om kwetsbare onderdelen zoals bumpers veilig te transporteren zonder dat de lak beschadigd raakt.
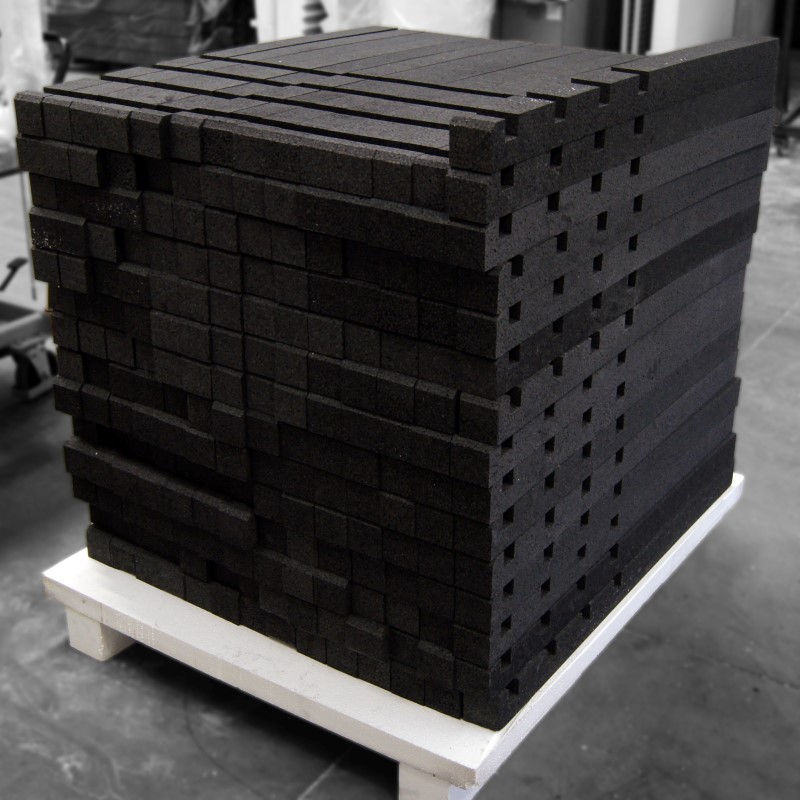
Schokdempende beschermprofielen in EPE.
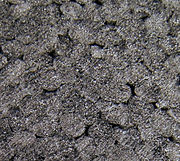
PUR (Polyurethane)
PU or polyurethane is a thermosetting polymer (meaning that it is not re-useable, because the structure is chemically altered, hence it does not melt to its raw material but chars). By these chemical alterations, PU can have different hardness and densities. The choice between them is made based on the application.
PU can easily be processed by contour sawing and milling, since this foam is characterised by its stiffness. Furthermore PU has a homogenous structure and because of this a smooth surface appears after milling. Contrary to EPS, PU is compatible with polyester, which makes this material well suited for coating with an end layer in polyester or coating (either on dissolvents, epoxy resin or glass fibre reinforced resin).
The characteristics of PU are that it maintains its form by a temperature between -180°C and 100°C. PIR is a modified version of PU with the same characteristics and which can't burn, which makes it very useful for insulation in insulation mantles. PIR can withstand temperatures between -200°C and 120°C and PIR-HT even to 200°C. Without end layer, PU discolours in the sunlight to a brown colour. PU absorbs very little water, making it resistant to rain. It has a strong form stability and doesn't rupture easily.

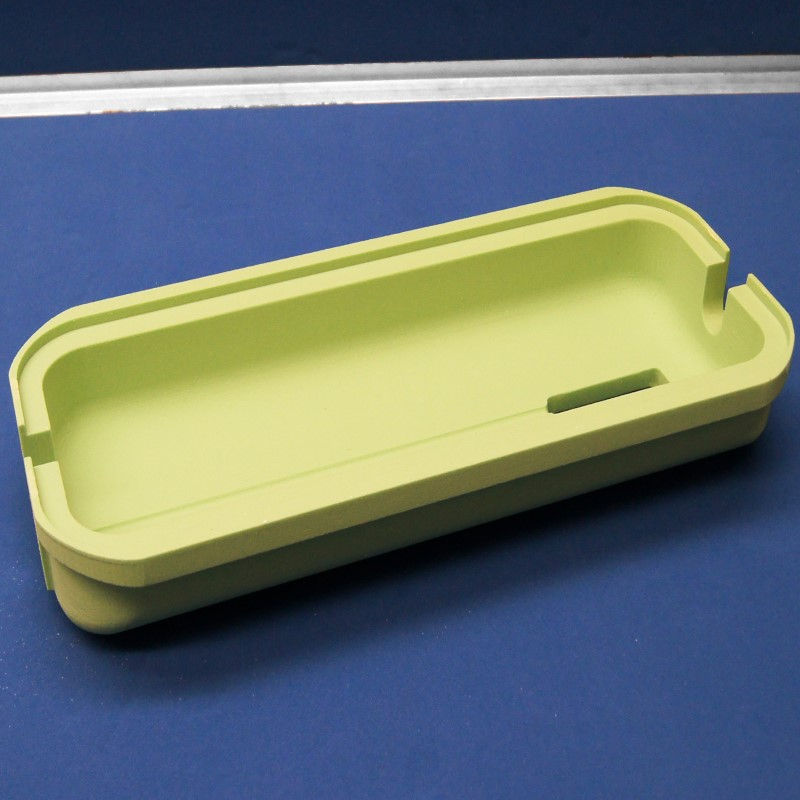


Betonbekisting voor zwembadrandsteen

Basismodel voor polyester mal op te maken voor automaat.

Barmeubel dat wordt gefreesd
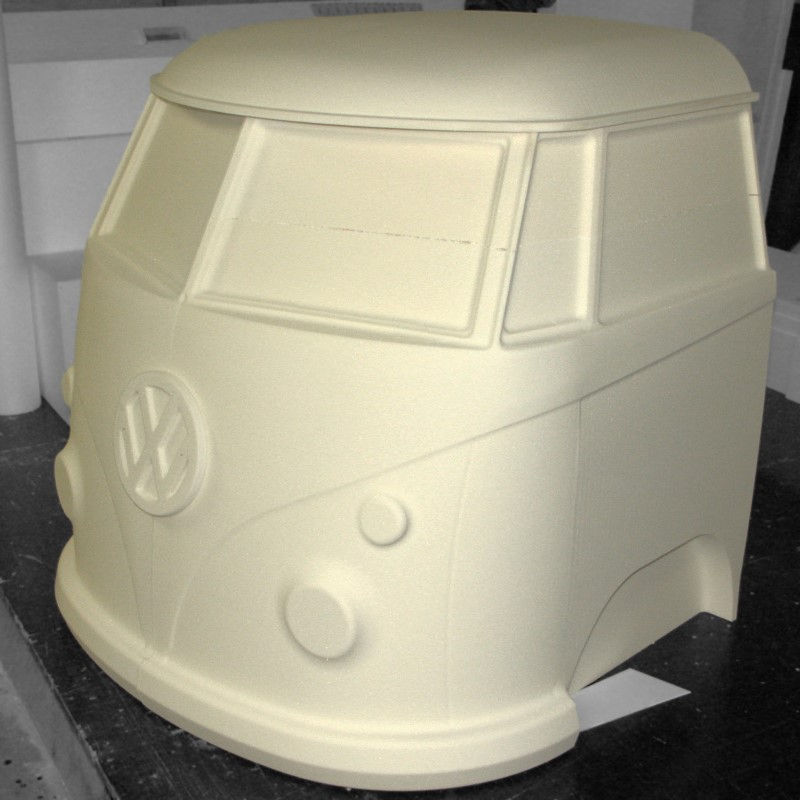
Gefreesde voorkant van volkswagenbusje
Raku-tool

Raku-tool is a ureole foam (a sort of heavy polyurethane) which is perfect for milling visual models and prototypes because of his hardness and smooth surface (comparable with MDF). Raku-tool is thus suited for purposes in which PUR doesn't give a detailed enough result (in surface structure or accuracy) or when the product mustn't be fragile. As is to be expected, Raku-tool is considerably more expensive than PU.
We use Raku-tool in a density of 240 (1m³ weights 240kg), 470 (1m³ weights 470kg) en 720 (1m³ weights 720kg). The density is chosen based on the product. Raku-tool can easily be contour sawn and milled.

Contour gefreesde letters 'immi-grand'

Prototype
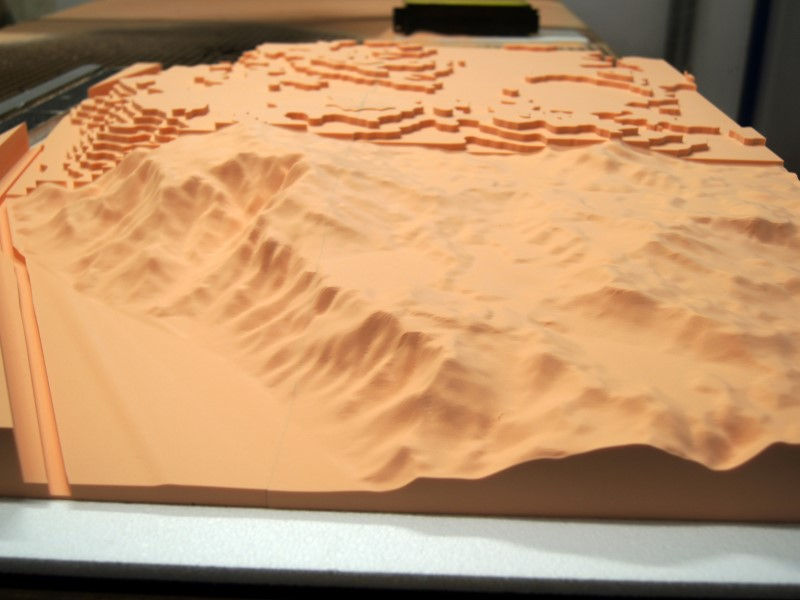
Gefreesde topografische kaart van een stuk van Tanzania
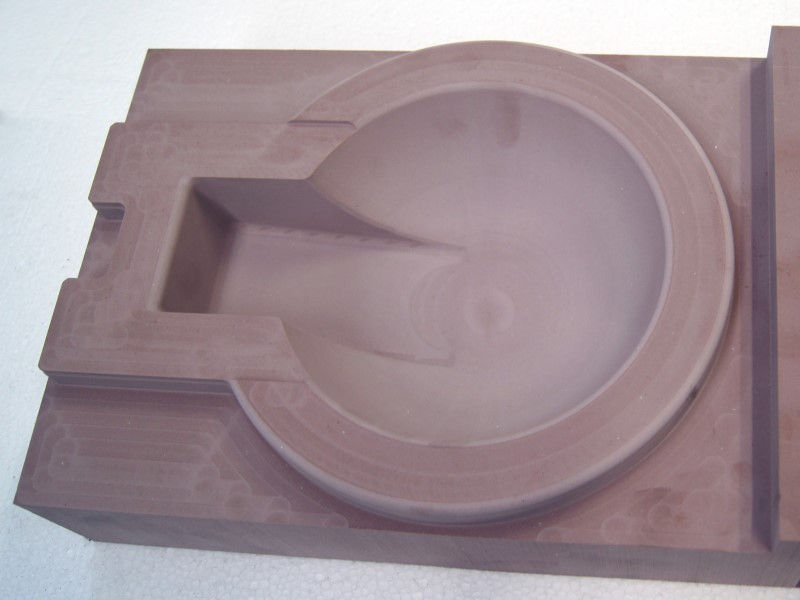
Prototype voor paardendrinkbak

Prototype voor drinkbasin
Polystyrene

Impact-resistant polystyrene (PS) is a thermoplastic that can be easily formed and folded by means of heat. Articles in PS cause no problems for health, are very stable and can be easily recycled. They are also extremely hygienic and may come directly in contact with food products. PS contains stabilisers that protect the material against fast ageing under the influence of oxygen and increased temperatures. Products can then last for years without the quality decreasing significantly. The thickness can vary from 0.3 mm to 5 mm. As far as the other dimensions of the products are concerned, they can vary from a few centimetres to sections of 3 m by 1.2 m. This impact-resistant polystyrene has a very broad area of application and because of its strength and its being washable is exceptionally well suited for prolonged and repeated use.
PS belongs to the category of the thermoplastics. It has a smooth surface and is easy to clean. It is biologically inert and it is resistant to most acids and bases. The material is stable after formation, hard and sturdy and fairly shock resistant. It is completely safe during production, processing and use in connection with food products (also for packaging). It can be made as foil in all possible thicknesses and in many colours. The normal implementation is mainly used, but it is also possible to use flame-extinguishing material.
We produce our own PS from the basic raw materials. Thus, it is always possible to adjust the correct product composition ourselves. We start with granules that are converted to foil by means of extruders and are then immediately processed or wound up on rolls for later processing. This further processing is done with thermo-moulding machines, after which the finishing with punching, cutting and milling machines will determine the appearance and the level of finishing of the products. Production-wastes and residue materials are immediately ground up and recycled as impact-resistant polystyrene. In most applications, where it has to do with 'non-food' applications, we already add up to 25% recycled material!
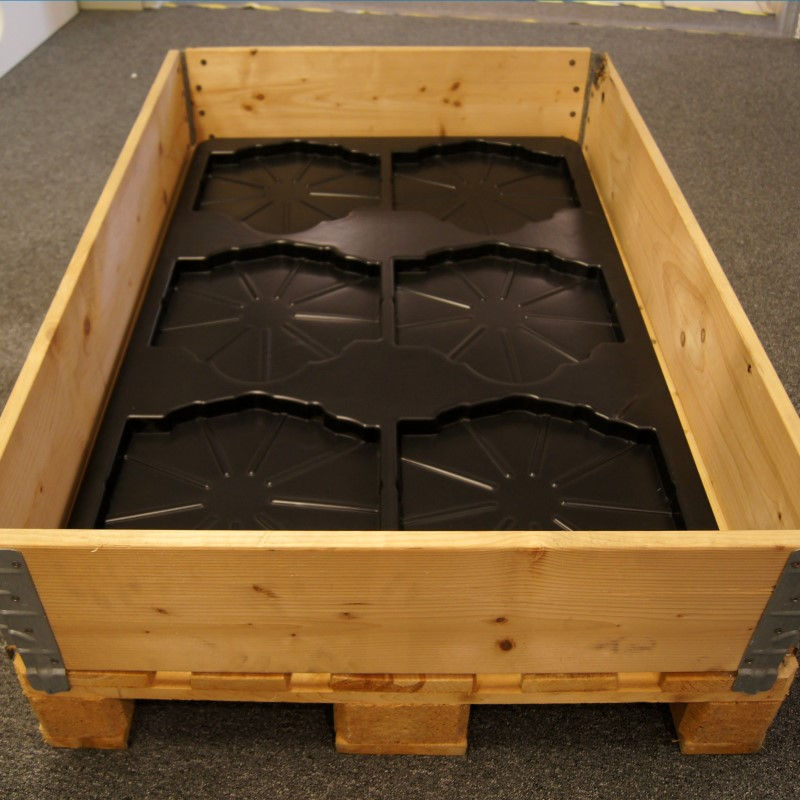
voor op pallets met opzetranden.


These biscuits were used as roof tiles for the Santa Claus house in Wijnegem Shopping Center (Belgium)

White PS tray for delivering hot meals door to door. The trays can be cleaned easily after usage.

Polypropylene

PP is a thermoplastic characterised by high impact resistance and a wide temperature range. This material can therefore be applied both at very low and at high temperatures. This plastic may come directly in contact with food products and is also exceptionally resistant to chemicals. For this reason product applications are made in the most diverse branches.
We produce our own PP from the basic raw materials. Starting with the granules, the material is thermoformed by extruders and moulding machines to the final product. Material thickness and composition as well as the level of finishing and the form can be adapted in accordance with the desired application and the desired final result. The parts produced can easily be processed further by using cutting, punching and milling machines. Residue and waste materials are immediately ground and recycled.
PP is elastic and resistant to wear, it is hygienic and easy to clean, it is very tough and tear-resistant. All this applies over a wide range of temperatures.


In de tray worden warme maaltijden vervoerd. Nadien kunnen ze makkelijk gereinigd worden.
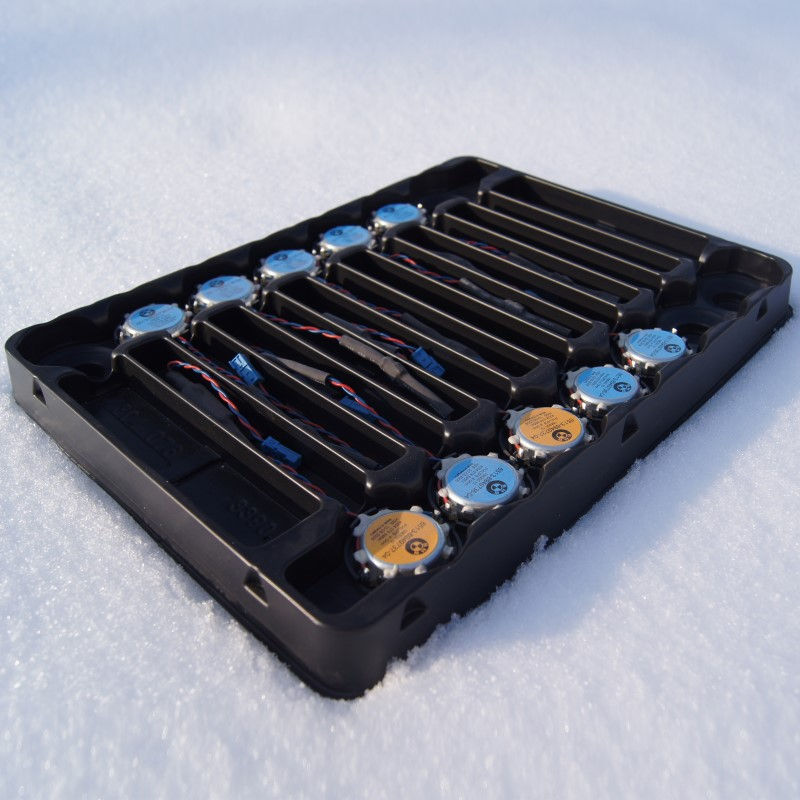
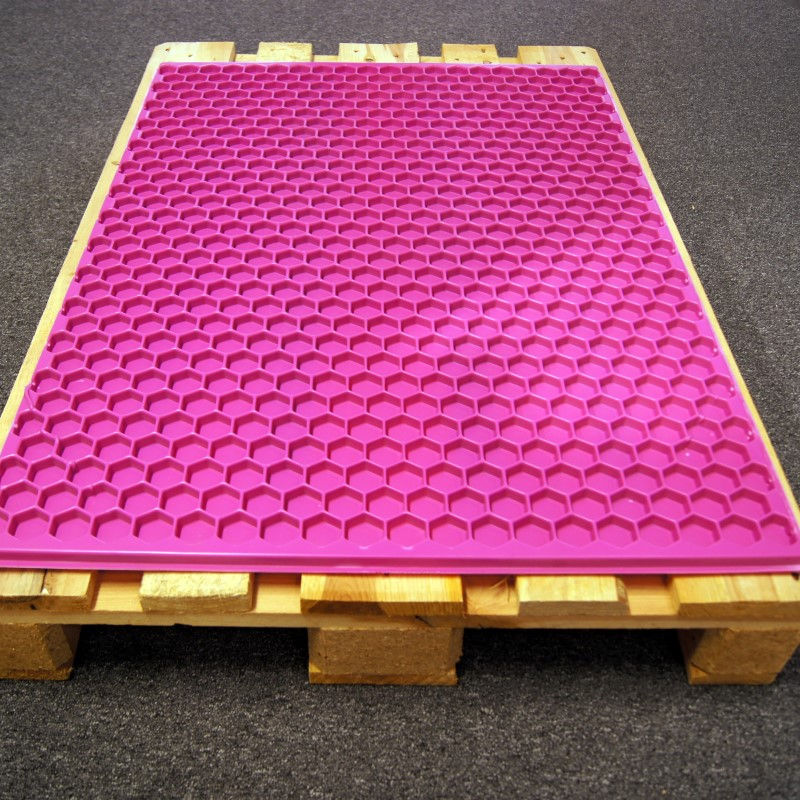

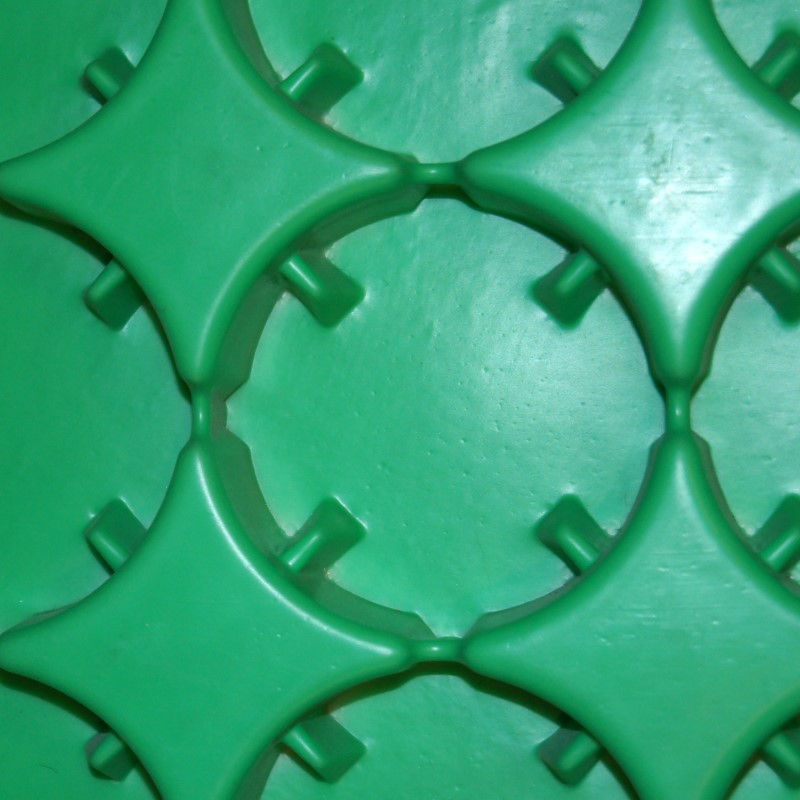
Other materials
To make your products, Twinplast uses different foams, both hard and soft, and solid plastics like: polyisocyanurate (PIR), Polyethylene (PE), Polyoxymethylene (POM), EVA, MDF, but also in other materials we can mill your products. You can also provide us with a material and we saw or mill it into the desired form!
The hardness, the density, the material type, color, fire resistance characteristics, moisture absorption, ... differs greatly between the different foams. The choice for using a particular foam or solid plastic is therefore determined by the purpose and requirements of the finished product.
Hard & soft foams and solid plastics are contour sawn or CNC milled into 3D design shapes for decoration, art works, etc, or fabricated into insulation, or made into shock resistant protection packaging.
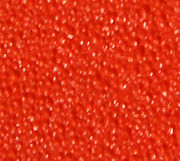
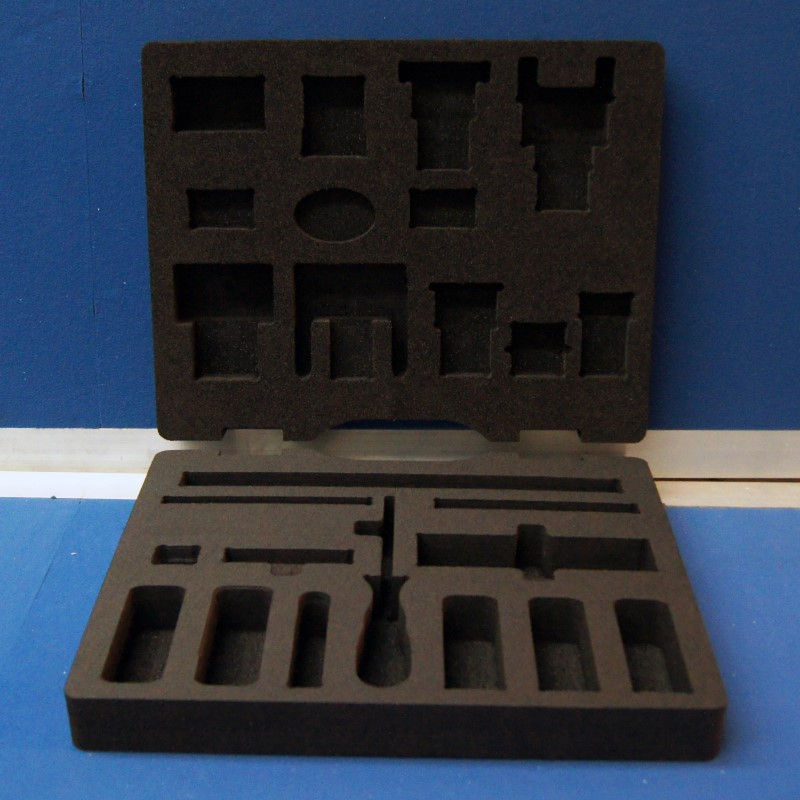
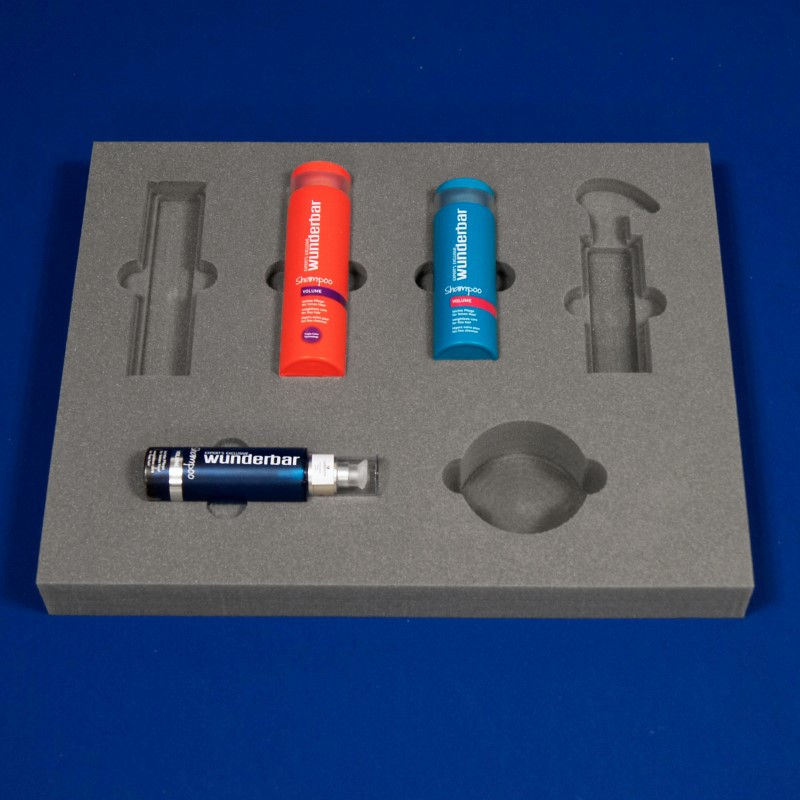

Basismodel voor kussen in zachtschuim





